Introduction
In the complex environment of the food industry, the Quality Assurance (QA) Manager plays a pivotal, yet often underestimated, role. Ensuring product safety, quality, and compliance requires meticulous oversight across numerous operational facets. However, the breadth of these responsibilities may not always be fully visible to colleagues outside the Quality Assurance function.
This potential disconnect in understanding can pose a challenge to the cohesive development and promotion of an organisation-wide food safety culture—a culture essential for every food business. Recognising the need for greater clarity and a practical approach to demonstrating the Quality Assurance professional’s daily contributions, this article introduces a valuable new resource.
The essential role of QA in the food industry
The QA Manager is central to upholding the rigorous standards that protect consumers and safeguard brand reputation. Their responsibilities extend significantly beyond routine checks, encompassing the strategic development and meticulous maintenance of critical systems.
This vital function includes establishing and maintaining detailed specifications for all raw materials, ingredients, and processes; ensuring all quality-related activities are underpinned by clear procedures and defined accountabilities; maintaining rigorous traceability records throughout the supply chain; and continually assessing products and operational processes against stringent internal and external standards.
Effective Quality Assurance management is directly and inextricably linked to preventing costly recalls, ensuring unwavering regulatory compliance, and building enduring consumer trust.
Bridging the QA communication gap for a stronger Food Safety Culture
Despite its importance, conveying the full scope of Quality Assurance work effectively within an organization can be challenging. Colleagues might not always grasp the intricate tasks essential for maintaining compliance and quality. Enhancing the visibility of these activities is therefore crucial. When the entire organization understands the quality department’s diligence, it fosters the shared responsibility necessary for a world-class food safety culture.
Clear communication and a collective understanding of the QA function empower all employees to contribute effectively to overarching safety and quality objectives.
Introducing the iMIS Food QA Activity Checklist
To facilitate greater transparency and provide a practical tool for professionals, we intoduced the iMIS Food Quality Assurnace Activity Checklist. This comprehensive checklist is designed to assist Quality Assurance Managers and food safety consultants in systematically tracking and documenting their activities across key areas:
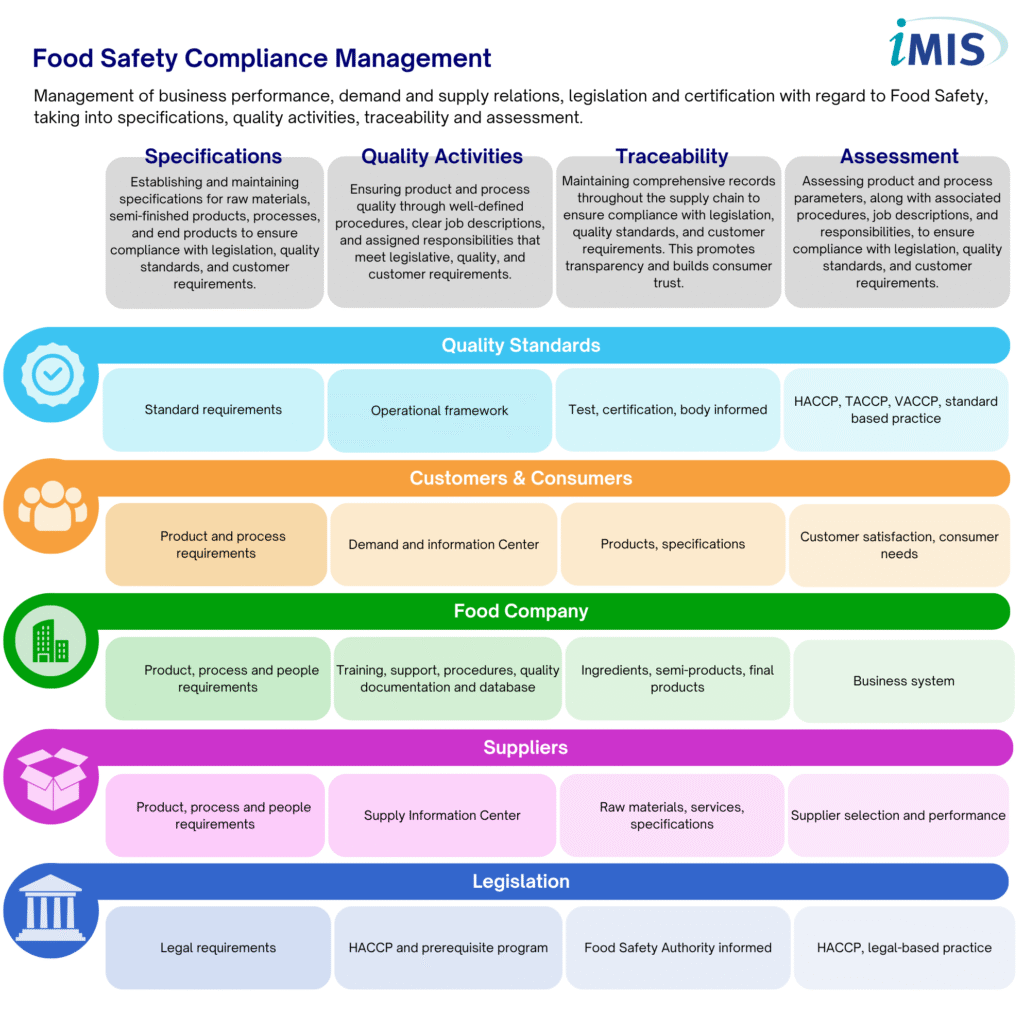
- Specifications: Managing specifications for raw materials, processes, and final products.
- Quality Activities: Overseeing procedures and responsibilities to ensure product and process quality.
- Traceability: Maintaining comprehensive supply chain records.
- Assessment: Evaluating product/process parameters and procedures.
- Quality Standards Compliance: Managing standards requirements, operational frameworks, and liaising with certification bodies.
- Customer & Consumer Focus: Addressing requirements and ensuring satisfaction.
- Food Company Operations: Including training, documentation, and product management.
- Supplier Management: Overseeing supplier selection, performance, and material specifications.
- Legislation: Ensuring compliance with legal requirements, HACCP, and regulatory communication.
Benefits of the checklist
This tool serves multiple purposes:
- Enhanced Visibility: It provides a clear overview of the diverse tasks.
- Improved Tracking: Ensures systematic monitoring and completion of critical activities.
- Facilitated Communication: Acts as a basis for discussing efforts and resource needs with management and other departments.
- Strengthened Food Safety Culture: Promotes broader organisational understanding and appreciation for processes.
Beyond the Checklist: A Holistic View of Food Assurance
The iMIS Food Checklist is a key instrument for operational transparency, and it also underpins a wider holistic approach to food assurance. True food system resilience is built by fostering a learning organization, a principle explored in depth in the article “Building Food System Resilience within a Learning Organization” by Ir. Cornelis van Elst et al.
This publication, aligning with the philosophy of our iMIS Food platform, shows how systems thinking and a proactive learning culture are vital for managing industry risks. Data from our checklist directly supports such a learning environment. To explore this comprehensive strategy further, we recommend their insights:
Conclusion
In essence, the iMIS Food Quality Assurance Activity Checklist is far more than just a tracking tool; it is a strategic resource dedicated to fostering operational transparency and championing the pivotal role of quality assurance within the challenging food industry.
By providing a clear, structured overview of vital responsibilities, it not only empowers individual professionals but, more importantly, fortifies an organization’s collective commitment to achieving the highest standards of food safety and quality excellence.
Related articles to The New QA Activity Checklist: Unlock Food Safety Transparency
Many customers and visitors to this page 'The New QA Activity Checklist: Unlock Food Safety Transparency' also viewed the articles and manuals listed below: